Blue Pearl 4
Culturing Abalone Half Pearls
Blue pearl 4, the story of New Zealand Eyris Pearl™
by Pam Hutchins FGAA
Wide Bay Valuation Services, Bundaberg
(Used with Permission)
Thanks, Pam, for suggesting that I add your informative paper to KariPearls.com.
Part 4
Part 1 Part 2 Part 3 Part 5
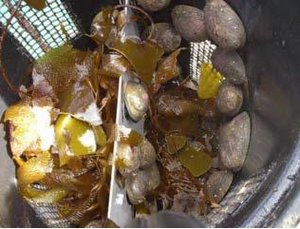 Fig. 13. Routine inspection and feeding of implanted abaloneBlue Pearl 4 |
During their life on the farm the paua are cared for by a dedicated team of aquaculturists. Each week, regardless of the weather the pearl vessel pulls up at the farm and the barrels that house the paua are lifted gently from the water. The paua are checked to see that they are in good health, their barrels cleaned, then in goes their favourite food, a variety of fresh seaweed.
With respect to the length of culture it is important to remember that in the winter months the mantle cells of the implanted abalone lay down (secrete) predominantly dark organic brown conchiolin. In contrast, the summer months are the time when the implanted abalone lay down translucent layers of nacre over the top of and within the previously deposited layers of conchyolin. One of the major factors controlling successful half-pearl cultivation in abalone is to ensure that the nucleation takes place at the correct period of each year, and that the pearls are harvested at that time of the year when best quality nacre is being secreted in thickest layers.
How nacre is deposited
Following implant, the abalone’s mantle starts to form the half-pearl by first secreting the first layer of conchyolin - a brown coloured organic layer – initially on the side of the implant and then as a thin layer covering the top of the implant. This conchyolin becomes the mortar into which layers of nacre are subsequently deposited. This sequence of deposition of conchyolin followed by aragonitic nacre is repeated successively to create the pearl. The content of conchyolin in the pearl is critical with respect to the strength of nacre, for the ideal incorporation of 1-5 wt % organic matter into the nacre will create a pearl that has a fracture toughness x 3000 greater than that of pure aragonite (CaCO3).
Harvest
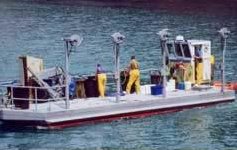 Fig. 14. The pearl farm work boat in action removing barrels of implanted abalone from the sea. Blue Pearl 4 |
Up to 36 months, and thousands of layers later, the resulting cultured half-pearl presents a lustre and iridescence that is almost magical to behold. The pearl harvest is a time of great excitement for the Eyris Blue Pearl™ team; the culmination of a minimum of two years work for everyone involved. Will this be a good harvest, or a great harvest? Will the next paua contain a perfect iridescent, brilliantly coloured, gem quality blue pearl? Nature has kept he pearly secret safe throughout this period, only at the pearl harvest are the results of her work revealed.
All staff on the farms will work long hours, even in bad weather, for the harvest must go ahead at a predetermined time when nacre secretion is at optimal levels. The grow-out areas are accessed by sea by specially designed work boats that are equipped with four hydraulic arms that are used to pull the barrels from the water, for the purposes of feeding, cleaning or harvesting.
the barrels that have been brought to the surface will have tags attached that show where the abalone came from, the diver who harvested the abalone, and barrel number, and details of when and where the abalone were implanted. Following the harvest of abalone from a barrel, the data is transferred both to the farm and head office so that it can be stored for bookkeeping, record and research purposes.
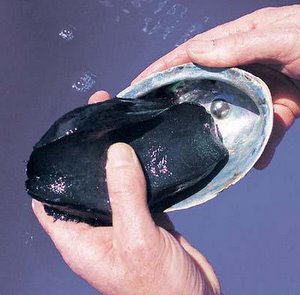 Fig. 15. Harvesting pearl bearing H.iris or paua.Blue Pearl 4 |
At harvest (Fig.14), the harvested ablaone is sacrificed, the valuable flesh of the abalone is removed from its shell and marketed to Asian gourmet food markets. The residual shell and its attached half-pearls are returned to shore where the cultured blisters are processed into saleable half-pearls, while the residual shell is on-sold for inlay and decorative purposes.
Removal and processing of pearls
Fig. 16. The results of several years cultivation. Blue Pearl 4
1st Photo - a 20 mm nacreous blister that took three years of cultivation in an abalone of small size.
2nd Photo - multiple smaller blisters in a larger abalone that will require two years of cultivation.Blue Pearl 4 |
Several manufacturing steps are required to transform the cultured blisters withing the shell of the abalone (Fig. 15) to saleable pearls. These steps involve:
1. The blister pearl is cut from the shell using a diamond saw.
2. The blister and adherent shell are split to facilitate removal of both the plastic implant and the ‘crusty’ layer of residual shell from the nacreous blister.
3. The insert is removed from the blister.
4. The nacreous blister is cleaned by washing it and blowing it dry with an air gun. This deliberate use of high pressure air will rapidly detect any weaknesses in the nacre.
5. All nacreous blisters making it through to this stage, are then measuremicrometer to determine the thickness of their nacre.
6. Blisters that attain the required thickness 0.3mm and over will be manufactured into and marketed as Eyris Blue Pearls™. In contrast, blisters having nacre of less than 0.3mm thickness will be manufactured and marketed Pacific Blue Pearls.
7. The blisters are then filled with colourless resin in two stages: a first stage that is allowed to harden for 48 hours, then a final fill before the blister is trimmed and base added.
8. The filled blister is then shaped (by removing excess nacre) to produce a symmetrical girdle of the optimal diameter and thickness. The machinery used to shape and polish the soon-to-be half-pearls are modified lapidary equipments. Dopping ensures that the finished pearls will be as symmetrical as possible.
9. The filled shaped blisters are then dried prior to their finishing by adhering a base to the blister. Paua shell mother-of-pearl backs are produced by a core drill. Anyadherent shell is removed by using 80 grit abrasive to only expose nacre. A 100 grit abrasive wheel is then used to regrind the girdle after the backing has been cemented to the filled blister. A 600 grit polish is used for the final finish of thegirdle to ensure that the pearl has the right thickness for setting. Residual conchyolin is removed from the external nacreous layer of the pearl by the careful application of tripoli on a rotating polishing mop.
10. The finished pearls are then sorted into commercial sizes and shapes (Fig. 17)
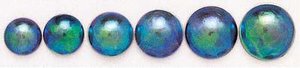
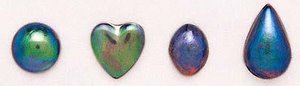
Fig. 17. Top - Common commercial sizes of round Eyris Blue Pearls™ ( 10-15 mm).Bottom - Range of available shapes of Eyris Blue Pearls™ L to R – round, heart, oval, drop.Blue Pearl 4End of blue pearl 4 - continue on to the next page.
Back to Part 1 after Blue Pearl 4
Back to Part 2
Back to Part 3
Ahead to Part 5.
Have you found an abalone pearl? Add a page about it here. We'd love to hear about it and see a photo.
Enjoy this page? Please pay it forward. Here's how...
Would you prefer to share this page with others by linking to it?
- Click on the HTML link code below.
- Copy and paste it, adding a note of your own, into your blog, a Web page, forums, a blog comment, your Facebook account, or anywhere that someone would find this page valuable.