Drills for Pearls in History
Here are two photos of drills for pearls that are being used today. Pearl drilling has been streamlined over the years. It is still an art, but the machines and processes have improved greatly. Read about historic methods here.
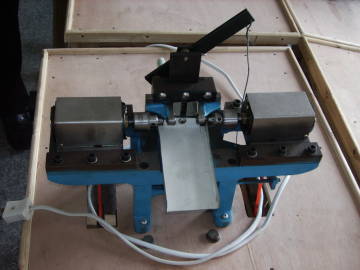
Modern Pearl Factory Drill
The following information is taken from Kunz and Stevenson's book about pearls and was published in 1908. Keep in mind that the methods described were in use one hundred years ago.
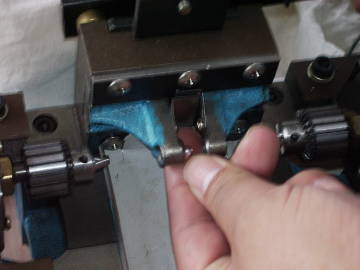
Modern Pearl Factory Drill Closeup
Pearl drilling is a most delicate operation. It is necessary that the drill points should have the proper shape, that is, should not be too tapering, but slightly blunt at the end, and turning somewhat in a V-shape. It is also important that the drill should be revolved with perfect regularity, so as not to jar or jolt the pearl, as this is likely to lead to the cracking of the pearl or to the breaking of the drill.
This latter happens not infrequently, and is due either to the structure of the pearl, the clogging of the drills for pearls, or to encountering a hard grain of sand enclosed in the pearl. Should the drill break in the pearl, it can best be removed by drilling from a point directly opposite, and slowly forcing the broken drill outward. This process requires great care in the regulation of the speed, and great exactness of direction in order to meet the broken drill accurately.
Pearl drilling was formerly a laborious process, and it was scarcely possible for a driller to perforate more than from forty to fifty pearls per day by means of the bow-drill operated by hand. Now, in 1908, by use of a "modern" machine, 1500 pearls of average size can be drilled without any difficulty in the same time.
Some of the most successful drills for pearls, especially of fine pearls, is the bow or fiddle-drill. The arm of this is made either of steel or of wood, with a strong cord stretched a across it in the style of an archer's bow. The drill is inserted in the end of a brass circular disk with a V-shaped groove on its edge, to admit of the string being passed entirely around it like a pulley, so that when the drill is placed on anything and held at the other side, and the bow is moved up and down, the wheel with the drill end rotates rapidly.
If the pearl is not properly secured, if the drill point it too irregular, if it is not properly centered, or if it is too rapidly rotated at the start, one or more layers of the pearl are likely to be broken, giving an irregular, ragged appearance. If, again, the drills for pearls are rotated too rapidly as they are leaving the other side of the pearl, one or more layers are occasionally forced off, and this in turn will produce a break on the pearl. It happens not infrequently that pearls are broken away on the surfaces at both drill holes if the workman is careless.
As pearls have become more valuable, only the most efficient workmen are employed in drilling them. Whereas formerly a drill hole would be half a millimeter in diameter, at present it is much smaller, and such drilling requires the greatest skill in manipulation. The use of these very fine drill holes is due principally to the fact that pearls have become so valuable that the slightest loss, even the fraction of a grain, would amount to a considerable sum in a necklace of large pearls.
When a pearl has been perforated with a very fine drill hole, the hole may be enlarged somewhat by using a slender copper wire, the fineness of the drill hole itself, charged with either diamond-dust, emery, or sand. When the wire thus charged is drawn in and out, the drill hole can be enlarged to any desired size.
A large pearl is held in the hand or secured in a wooden block, or else it is held in a small pair of forceps with a rounded, cup-shaped receptacle at the end, which is usually lined with chamois leather and is pierced with a hole through the center. This hole serves as a guide for the drills for pearls, directing it while the pearl is being perforated. Adjustable cups or forceps with cup-like ends of every size are necessary, according to the size of the pearl; and in order that it may be properly seen, it is requisite that the pearl should always be larger than the cup in which it is placed.
The poorest part or spot is selected to form the beginning of the drill hole made by drills for pearls. The pearl is placed in a pair of calipers with a circular disk, one end of the caliper being placed on the spot to be pierced, the other end naturally touching exactly opposite, the pearl absolutely centering it. As these caliper ends have been rubbed with either rouge, lampblack, or some colored substance that will readily rub off, these two spots of color remain on the pearl and serve as a guide for the driller.
The drill end is then placed on the pearl, and the bow moved up and down; and so rapid is this work that five pearls weighing fifteen grains each can be drilled with the greatest care in less than one hour's time. Of small pearls, weighing about one grain, as many as fifty have been drilled in less than one hour by the hand drills for pearls method.
Many of the thinnest and best drills for pearls are made out of thin steel needles. These are ground flat by means of a small carborundum wheel, so as to have two flat sides. They are then thin pointed, and with a V-shaped edge. These prevent the drill from clogging up, allowing the fine dust to pass upward and outward readily, and the hard steel almost invariably penetrates the central core of the pearl, no matter how hard or tough this may be. The needle-drill is then secured in a small chuck attached to the brass revolving wheel.
Some recommend lubricating a drill with milk when it is employed for piercing a pearl, but a well-made drill, that allows the dust to escape as it is formed, does not require this treatment. The drills for pearls should always be made to revolve quite slowly so that no unnecessary heat may be generated by friction to injure the color of the pearl and also to avoid the possibility of the drills for pearls becoming clogged by the pearl-dust.
By means of centering calipers or markers, the driller, especially in the drilling of a large pearl, will generally drill first from one end, and then reverse the pearl and drill from the other end, meeting absolutely in the center. This prevents the breaking of the outer layer of the pearl. A skillful workman can, by turning the pearl, so operated the calipers that the true center can be obtained, even if the pearl is not absolutely round, and the drill holes made by the drills for pearls so centered that the irregularity of the pearl is less apparent.
When the pearl has been half drilled through from one side, considerable caution is necessary in drilling from the other, that when the two drill holes are about meeting the drill be not revolved too quickly, as the clogging is likely to crack the pearl or break the drills for pearls. If the pearl is only to be drilled by drills for pearls one fourth or one half through, the depth can always be gauged by watching the drill-end, first, by measuring the drill-end itself, and secondly, by noting to what part of it pearl-powder adheres.
Pearls are more easily manipulated than any other gems. They are also more easily damaged. Still, when properly treated by the workman, there is no material that offers him more satisfactory results than the pearl, if good judgment be used.
Drillers occasionally find that when the drill in drills for pearls reaches the center of the pearl, there is a harp click, the pearl often breaking at this point. This is evidently due to the fact that a harder kernel may exist in the center, such as a tiny grain of sand, which can turn the drill-point; or else the resistance may cause the tiny drills for pearls to break.
When a pearl is cracked by a blow or by some accident, it is customary to drill it at the end of the largest crack; this method prevents the crack from extending in that direction. these fissures are sometimes partly filled by means of a solution, and may not be visible at the time when the pearl is bought, but they are liable to appear later.
The most primitive known drills were the flint drills, made by the North American Indians by chipping chert or flint-like minerals to a fine point. With these rude instruments a large, irregular hole was made, which generally measured several times the diameter of the fine drill hole made by a modern pearl driller with improved drills for pearls. The Indians are also said to have used hot copper drills for pearls.
The earliest, and still a very general and perhaps the best way of drilling pearls, is by means of the bow or fiddle-drill. This method has been used in a more or less perfected form by all the aboriginal peoples of the New World from Iceland to Tierra del Fuego. But as none of these people were familiar with fine, hard steel, they scarcely ever succeeded in making drill holes as fine as those that can be produced by the use of tempered steel. By the latter means, pearls half an inch in diameter are often drilled entirely though with an aperture no larger than a thin bit of straw.
See inside a modern day pearl factory after reading about drills for pearls.
Search here.
Enjoy this page? Please pay it forward. Here's how...
Would you prefer to share this page with others by linking to it?
- Click on the HTML link code below.
- Copy and paste it, adding a note of your own, into your blog, a Web page, forums, a blog comment, your Facebook account, or anywhere that someone would find this page valuable.